Shipping containers are a lifeblood of global trade. They provide a foundation for efficient and cost-effective import and export operations around the world which is why they make up 20% of all Maritime cargo. But what do these metal boxes look like before they’re filled with products and shipped away? Let’s take a closer look at how shipping containers are made, the process from start to finish, as well as where they come from and what materials are used to create them.
What is a shipping container made from?
Shipping containers are primarily made of steel. They are manufactured in factories to strict specifications, which include the dimensions and shape of each container. Most modern shipping containers have a smooth surface on the outside – a simple box that measures 8 feet wide by 8 feet tall 40 or 20 feet long depending on its type (standard sizes allow for more flexibility in transportation, storage and loading). The containers are then loaded onto trucks or trains to be transported around the world.
How does a shipping container get made?
This is where things start to get interesting – and complicated. Like other manufactured products, one of the first steps is designing an appropriate steel shape that will accommodate whatever it needs to carry. Then, the steel is formed into a container using automated machinery. This process can be done one of two ways; hot or cold forming.
Hot-formed containers are manufactured by heating coils of sheet metal and bending them around forms to create box shapes that have “memory.” The edges won’t sag after repeated use like many products made with cold-formed steel. They are generally more expensive than cold-formed containers because of the additional steps and materials needed to create them, but they also provide a stronger product that can be used many times over – perfect for harsh weather conditions and continuous shipping around the globe.
This process also allows for multiple containers to be stacked on top of one another without breaking.
Cold-formed containers use pressure and high speeds to push mental through a dye, which is basically an opening in the sheet metal. The edges of each container are sharp and often need to be rolled or “drawn” so they aren’t dangerous to workers.
The Shipping Container Repurposed.
Instant Sea Containers are a proudly Western Australian owned and operated business. With demonstrated experience, we have been involved in the design, manufacture, sale and hire of standard containers and container style modular buildings for over 6 years.
As a result, we have quickly become an industry leader. We offer a wide range of standard sea containers and converted shipping container buildings available for immediate delivery.
Whatever the requirements – We Can Solve it in an Instant!
For those looking for sea container for sale Perth, Instant Sea Containers is your go-to provider. Our range of sea container sales in Perth offers solutions tailored to your unique needs, ensuring quality and reliability. Visit us at 18 Rogers Way, Landsdale WA 6065 or call 08 9415 0720 for assistance. Our 24/7 customer support at 1300 464 214 is always ready to help you find the perfect sea container for sale in Perth for your project.
Frequently Asked Questions
What materials are used to make shipping containers?
Shipping containers are primarily made of steel, designed to meet strict specifications for durability, efficiency in transportation, and ease of loading.
How are shipping containers manufactured?
The manufacturing process involves designing a steel shape, which is then formed into a container using automated machinery. This can be done through hot or cold forming, with hot-formed containers offering enhanced durability and strength.
What are the standard sizes of shipping post containers?
Standard shipping containers typically measure 8 feet in width and height, with lengths of 40 or 20 feet, allowing for flexibility in transportation and storage.
Why are shipping containers repurposed?
Due to their durability and modular design, shipping containers are repurposed for various uses, including office spaces, pop-up shops, and homes, offering a sustainable solution by reducing waste.
How can shipping containers be customized?
Shipping containers can be customized with shelving, temperature control, windows, doors, and specific finishes to serve various purposes, from storage solutions to commercial and residential spaces.
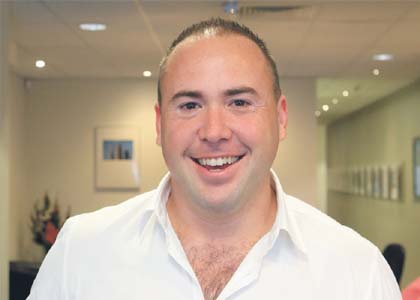
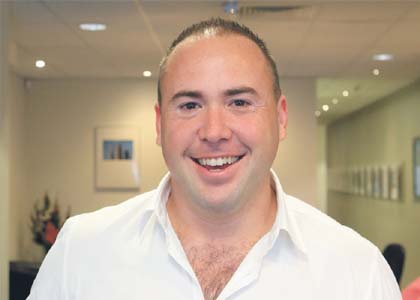
Managing Director at Instant Sea Containers
Scott Rawson is the Managing Director of the Instant Products Group, a specialist group of companies that offer portable building solutions, including sea containers, transportable offices, and portable sanitation products.